Understanding Basket Strainers: Types, advantages, and applications in fluid systems
Basket Strainers
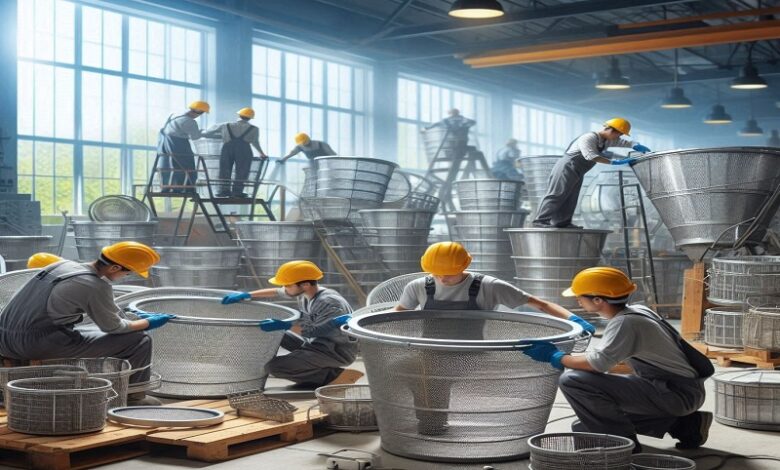
The basket strainer forms part of the fluid system with the capability of capturing debris, dirt, and other contaminants that can be found in liquids and gases. Consequently, it keeps the running pipework and machines smoother. With basket strainers, equipment such as pumps and valves will work and serve for much longer periods. Today, basket strainers come in various designs to meet specific requirements in terms of flow and specific operation in such places as chemical processing, water treatment, and HVAC systems. A basket strainer manufacturer produces filtration systems designed to effectively capture and remove debris from liquids, ensuring optimal performance and protection for pipelines and machinery across various industries. In this article we will discuss all the types of basket strainers, their key advantages, and how they are the most appropriate for particular applications, thus highlighting their utility as integral parts in fluid management.
Exploring uses of basket strainers
A basket strainer is a mechanical device designed to filter out debris, particles, and other contaminants from liquids or gases within pipelines or fluid systems. The latter uses a perforated or mesh basket to capture unwanted material as the fluid flows through the strainer-this prevents blockages, damage, and wear to downstream equipment. Basket strainers are used in almost all industries, such as chemical processing, water treatment, oil and gas, or in HVAC systems. It prevents the dirt and debris from pumps, valves, and other equipment necessary for the perfect working state and is easy to clean or replace.
How is Basket strainer manufactured?
High-grade materials such as stainless steel, carbon steel, or other alloys resistant to corrosion are used in mass production of basket strainers for specific applications and fluids. The first fabrication aspect of this process is the body or housing, usually a welded or cast structure designed for pressure resistance in fluid flow. The actual basket, the core element of filtration, is made of a fine mesh or perforated material, shaped and designed such that it fits inside the housing. The material used for this mesh is usually stainless steel due to its side-by-side strength and resistance to corrosion. Assembled strainer housing, basket, and internal parts would be subjected to performance and structural integrity testing for filtration efficiency as required by the industry. A few will have cleaning ports or drain valves for easy maintenance.
Explain different types of Basket strainer
Basket strainers exist in several different types, suited to particular applications and flow requirements. Probably the most commonly used types are single basket strainers, which have one filtration basket, and are great for easy, low-cost filtering in low- to medium-flow systems. Double basket strainers have two baskets so one may be constantly under service while the other is cleaned or replaced; thus, they make excellent choices for applications that insist on getting the flow. Basket Strainers are a compact, space saving design and are generally used in smaller pipelines or applications with a reduced footprint. Others include the Tee Strainer having housed the basket within a T-shaped pipe and suited to some flexibility in tight spaces. Pot Strainers feature a cylindrical body that is used in higher capacity filtration, generally applied in larger industrial systems. Automatic Basket Strainers have the added feature of having a self-cleaning mechanism so that during its operation, debris is automatically removed and should not be maintained manually. Each type of basket strainer has to be chosen based on the application at hand, alongside consideration of flow rates and level of needed maintenance on the system.
What are key advantages of using Basket strainer
The Key Benefits of a Basket Strainer include: Its Effectiveness in Protecting Fragile Equipment and Machinery from Damage by Debris, Sediment, and Other Contaminants Found in Fluid Systems. The removal of particulate from the flow by basket strainers allows pumps, valves, and other downstream components to stay efficient and long lived with lessened maintenance and downtime costs. They feature easy installation, maintenance, and cleanability so that they may prove to be economical for filtration in different fields, such as chemical processing, water treatment, and HVAC. Design flexibility, like single or double baskets, and automatic cleaning, thus enable basket strainers for varied applications with reliability even in low or high-pressure systems. Additionally, as they have a strong structure along with the capability of withstanding a high flow rate, they can be used for demanding applications.
With all this in mind, Basket Strainers are essential filtration devices that prevent contaminants within fluid systems from causing damage, or total system failure, so that this machinery can perform effectively and for longer periods of time. Built into stainless steel and many other corrosion-resistant materials, they vary in type to fit a range of applications, from single basket designs, suitable for simple filtering, to more complex automatic systems for constant operation. Their debris removal ability reduces maintenance costs, minimizes downtime, and enhances the reliability of important equipment in industries that include chemical processing, water treatment, and oil and gas. In short, the flexibility, ease of maintenance, and cost-effectiveness of basket strainers make it an indispensable element in many fluid management systems.